
Essential Guide to Product Production Strategies
Deciding on the right production strategy for a product can significantly influence its success in the market. A well-thought-out product development process involves understanding various manufacturing decisions that cater to production efficiency, cost-effectiveness, and market demand. This guide will explore essential production methods, highlight the importance of sustainability in manufacturing, and discuss the innovative trends shaping the industry.
As businesses strive to launch products that meet consumer expectations, they must consider product design considerations, assess cost analysis for production, and utilize market research for products effectively. In this guide, we will break down different facets of production strategies that any management team can adopt for not just product launches, but also for long-term sustainability and growth.
The following sections will delve into the various aspects of production methods, market demand assessments, and technological impacts on production, along with practical tips to enhance efficiency. You will also find valuable insights on making informed decisions that align with your company’s operational goals and sustainability practices.
Understanding Production Methods for Effective Strategy
Exploring different production methods is vital in determining the best approach for any product line, such as the eco-friendly water bottles in our example. Each method bears unique advantages and operational requirements:
Evaluating Different Production Techniques
When launching a new product, teams should assess multiple manufacturing techniques that include:
1. Utilizing Recycled Materials: This approach not only reduces waste but also minimizes costs associated with raw material procurement. Companies must evaluate the performance and consumer demand for these products to ensure market fit.
2. Partnering with Local Manufacturers: By collaborating with local suppliers, companies can lower shipping emissions and costs while supporting community economies. It’s essential to conduct a thorough vendor selection process to choose partners that align with sustainability goals.
3. Advanced Manufacturing Technologies: Incorporating innovations such as automation or robotics can optimize production efficiency while ensuring product quality. This requires understanding the technology impact on production and optimizing production capacity assessment.
Cost Analysis and Supply Chain Management
Analyzing production costs is vital for ensuring the product's profitability. This analysis covers:
1. Production Costs Analysis: Understanding fixed versus variable costs helps in setting product pricing strategically. Being aware of budget constraints is crucial.
2. Supply Chain Optimization: Evaluate supply chain mechanics to identify bottlenecks and enhance resource allocation in production. Effective inventory management in production can reduce overstocking and ensure timely delivery.
3. Lean Manufacturing Principles: Implementing methods to reduce waste and improve efficiency significantly affects overall production performance.
Market Demand Assessment and Product Lifecycle
The relationship between market demand and effective production strategies is intricate. Understanding demand can guide production planning and workflow design decisions.
Market Research and Consumer Behavior
Conducting thorough market research for products enables companies to gauge customer needs accurately:
1. Customer Feedback Incorporation: Utilizing voice of customer analysis aids in refining product features. Engaging with the customer base helps in product feature prioritization.
2. Demand Forecasting Techniques: Employ model forecasting to predict market tendencies for better inventory decisions. This includes embracing trend analysis in product development.
3. Product Testing Methods: Testing prototypes helps to mitigate risks and align the product with consumer expectations before full-scale production.
Managing Product Lifecycle
Understanding the product lifecycle management can optimize resources and anticipate production changes. Companies need to:
1. Analyze Lifecycle Stages: Recognize each stage of the product lifecycle from introduction to decline. This leads to informed decisions about product updates and production capacity.
2. Implement Continuous Improvement in Production: Fostering a culture of innovation and adaptation can help refine production processes, maintaining relevance and competitiveness.
3. Evaluate Compliance in Manufacturing: Staying aligned with safety and regulatory standards ensures sustainable and responsible production practices.
Risk Management and Equipment Selection
Risk is inherent in production. Identifying and mitigating risks can significantly enhance production stability:
Effective Risk Management in Production
1. Production Risk Assessments: Perform regular assessments to identify potential disruptions in workflow and supply chain interactions.
2. Equipment Selection: Choose reliable and efficient systems that minimize downtime. Consideration of equipment reliability and maintenance strategies can boost operational efficiency.
3. Robotics and Automation in Production: Embracing automation can effectively reduce labor costs while improving consistency in manufacturing quality.
Operational Efficiency Enhancement
Lastly, focusing on operational efficiency through data analysis and strategic planning is essential:
1. Process Improvement Techniques: Implement process mapping and workflow design to identify inefficiencies and improve the flow of operations.
2. Performance Benchmarking: Set performance metrics and compare them across production cycles to ensure continual enhancement in methods.
3. Just-in-Time Production: Adopt just-in-time production methods to reduce lead times and align production directly with market demand trends.
Conclusion: Launch Strategies and Future Innovations
In conclusion, developing effective product launch strategies requires a thorough understanding of the production process. Coupling comprehensive market demand assessments with strategic manufacturing decisions can significantly impact overall success. Emphasizing sustainability, innovation, and operational efficiency while adapting to market dynamics prepares organizations not just for today’s market but future challenges as well.
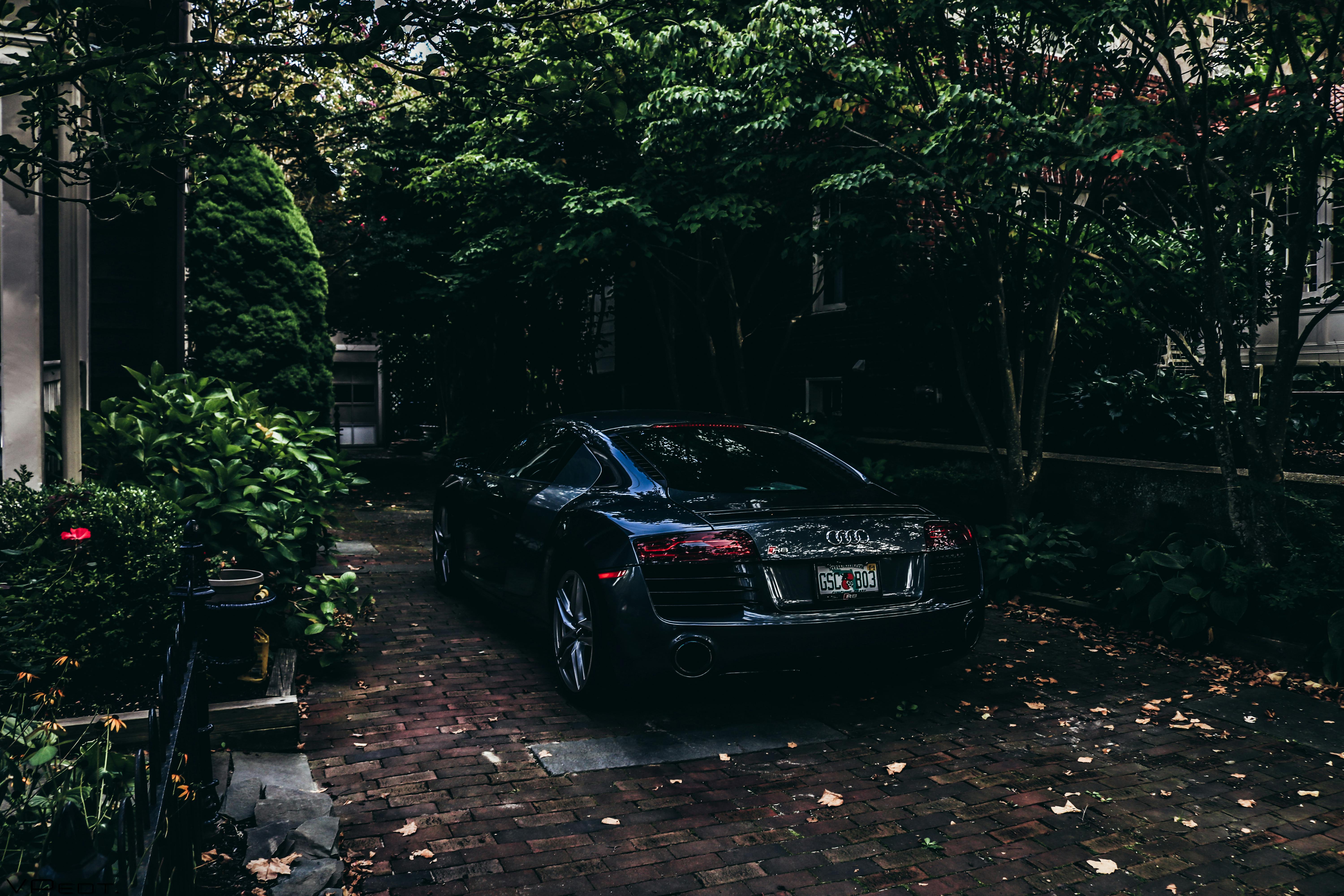
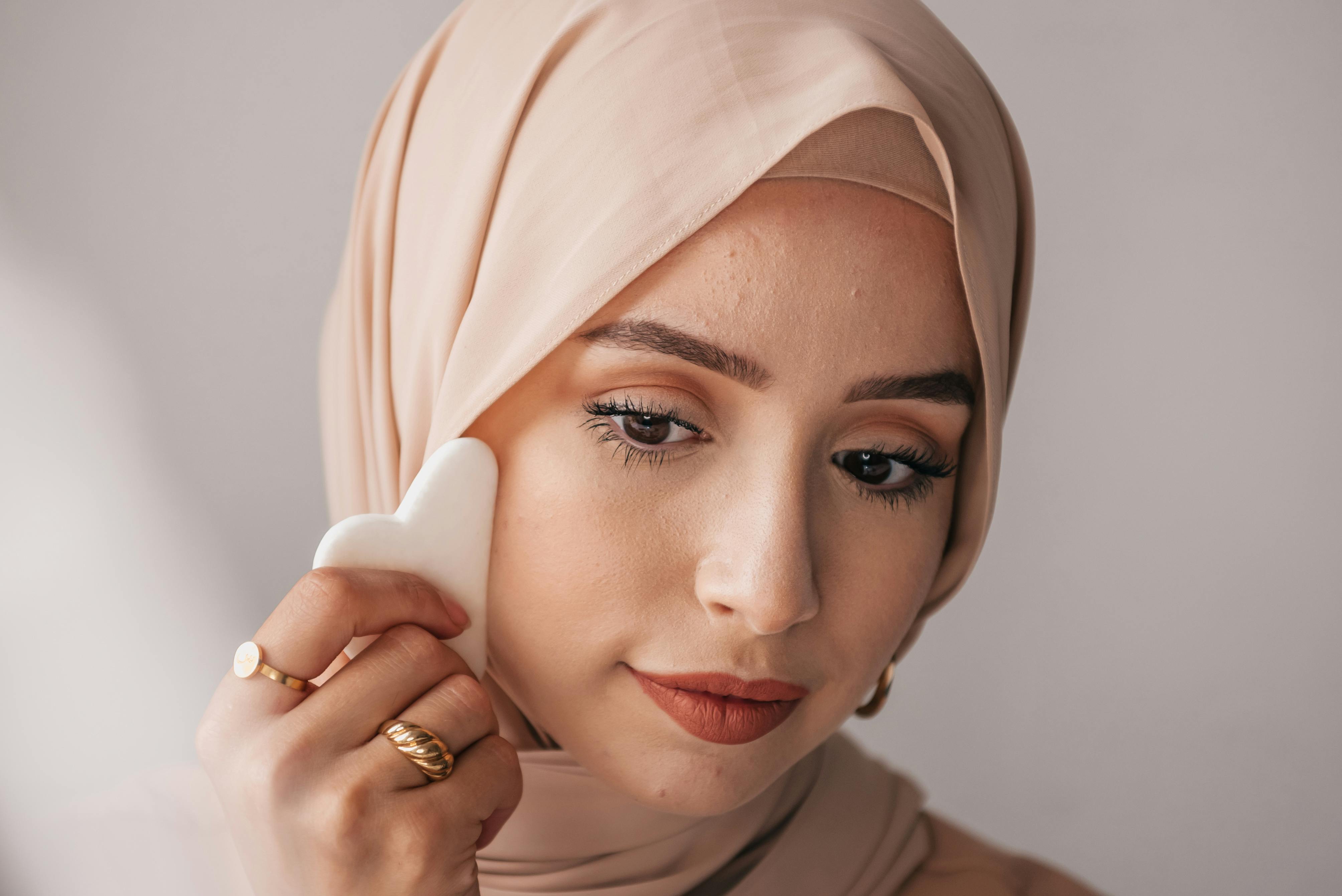